I. Project Background
The riverbanks of an urban inland river were in really bad shape. They got badly damaged and even collapsed. This happened because the water had been flowing and wearing them away for a long time. Also, the construction work going on around the river didn’t help. This was a big problem! It put the lives and property of the people living nearby in danger. And it wasn’t just people – the river’s environment got hurt too. So, to fix this, they decided to use gabion retaining wall technology to make the river better.
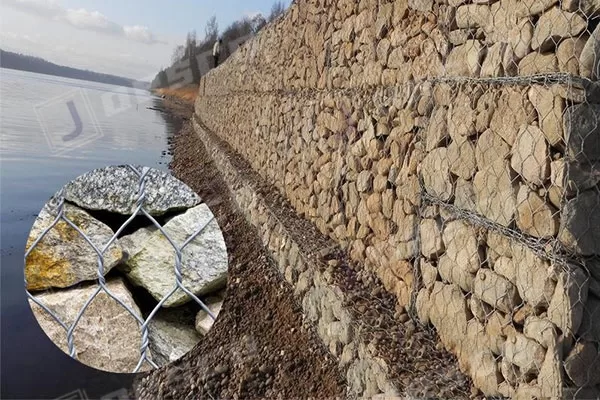
II. Design Scheme
Wall Material: Looking at the river channel and what it’s like there, they picked galvanized steel wire mesh for the gabion wall. This stuff is great because it doesn’t rust easily and doesn’t cost too much.
Structural Design: The retaining wall was made in a trapezoidal shape. The bottom was 3 meters wide, the top was 1 meter wide, and it was 4 meters tall.
The gabion cage was 2 meters long, 1 meter wide, and 1 meter high. The holes in the mesh were 60mm by 60mm.
For the foundation, they used a concrete cushion layer that was 0.5 meters thick. They put this layer 1.5 meters down into the riverbed.
Drainage Design: They put in PVC drainage pipes that were 50mm in diameter. They put one of these pipes every 2 meters on the wall. Inside the wall, they filled it with gravel to act as a filter.
III. Construction Process
Site Preparation: First, they had to clean up the parts of the riverbank that had collapsed. They got rid of loose soil, weeds, garbage, and anything else that was in the way. Then, they used a total station to do really careful measuring and marking. This was to figure out exactly where the retaining wall was going to go and where they needed to dig for the foundation. They also set up control piles and benchmarks to help them build everything right later on.
Foundation Construction: They used an excavator to dig the foundation. Once they dug down to the right depth that the design said, they went in by hand to make the bottom nice and flat and level. They had to make sure it was just right according to the design. Then, they poured the concrete cushion layer. When they were pouring the concrete, they were really careful about how much of each thing was in the mix and how runny it was. They used a vibrating rod to make sure the concrete was all packed in tight and strong.
Wall Assembly and Installation: They cut and bent the galvanized steel wire mesh sheets to the right size on a flat area. Then, they connected them into gabion cages using binding wires every 200mm to make sure they were really connected well. They started putting the gabion cages in from the foundation, layer by layer. When they were putting them in, they used a crane to lift the cages to the right spots. This was to make sure the cages were straight up and down and flat. They put the cages next to each other in a way that they kind of overlapped a bit. This made the wall stronger and more together. After each layer of cages was in place, they used measuring tools to check everything again and make sure it was all in the right place and not too far off.
Filling Stone Construction: They chose granite stones that were between 200 – 300mm big to fill the cages. They filled the cages by hand and with a loader. First, they put a 300mm-thick layer of smaller crushed stones at the bottom of the cage to make it level. Then, they started filling in the big stones. While they were filling, they put the stones in by hand to make sure they were all packed in tight and fit together well. They left 200mm of space from the top of the cage. Then, they used smaller crushed stones to fill that space and make the top of the wall flat and stable. While they were filling, they used a small vibrating rod to shake the stones. This made the stones fit together even better and made the wall stronger so it could hold more weight.